Two months ago we posted part 1 of our project Jensen speaker rebuild for our original 1964 pre-CBS Fender Super Reverb. The amp has original transformers and used to sound wonderful – but the original Jensen speakers were in rough shape. The cones had tears, and the magnets on two of the speakers had shifted off-center, causing the voice coils to freeze and no longer produce any sound.
Because the amplifier is collectible, we wanted to preserve as much of the originality of the amp as possible, so we opted to have the speakers repaired and reconed. Reconing a speaker is the process of removing the actual cone assembly – which contains the speaker’s voice coil, gasket and spider assembly, and replacing it with new materials. Cone rebuild kits vary in type and quality and we’ve trusted our amp speaker upgrades to the team at Weber in the past– so we knew that they would be the team to work with for the speaker repairs.
As expected, the four 10-inch Jensen speakers were returned and sound fantastic. But it wasn’t immediate…There was break-in time of playing for several hours that was required before the full and great frequency response and nice feel and compression returned. It was well worth it.
But what I was interested in learning about was the actual process of how reconing and repairing the speakers was done. Brian Spane of Weber was kind enough to provide some insight into the process. With over 10
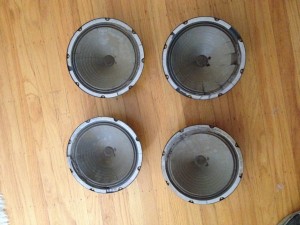
years of experience doing new speaker builds and 8 years on rebuilds at Weber, Brian has seen and worked on just about any musical instrument speaker you could imagine.
Speakers can degrade and become damaged in any number of ways, presenting a number of challenges with rebuilds. “I think the most important factor to reconing is the experience and knowledge gained over time,” Brian shared.
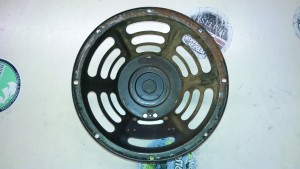
He added that the materials are of course important and that the ones used for reconing consist of the same cone materials used for their speakers – designs that were created to replicate the tone and response of the original speakers.
In the case of two of four Jensen speakers, once the old cone material was removed from the frame, Brian had to realign the speakers so that the cone assembly could be properly re-centered. The magnets were then demagnetized. Once the new cone assembly is repositioned and the repaired, the new magnets are re-energized and the speaker cone glued and and
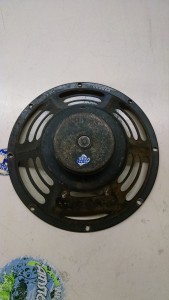
final assembly completed. “We have some tools that were machined for us, for our builds, that I use on recones as needed,” Brian added.
The cost of reconing a USA Jensen speaker (they do not recone the reissue Italian Jensens) is $65 for a 10-inch model. This service includes demagnetizing the speaker, cleaning, remagnetizing, and replacement of all “soft parts” which consist of the cone, gasket, and voice coil assemblies. If any of the speaker terminals are damaged,
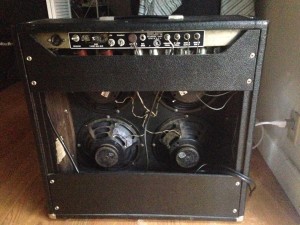
Weber will replace those as well in addition to conducting full testing of the speaker upon completion.
An additional $25 charge is required if the magnet and pole assembly needs realignment or replacement (usually the case if the cone is frozen and won’t move). Two of my Jensens suffered from this plight.Visit the Weber recone services page for information on how to proceed if you’re interested in restoring your old speaker.
Weber emphasized that since the company has experience with hand-building speakers for nearly 20 years of various designs and types, they are highly capable of taking on recone and rebuilding work from start to finish.
When deciding between speaker replacement or reconing for an upgrade, often a new speaker replacement is the easiest and certainly most versatile way to go – there’s a plethora of choices out there in speakers. You may want a design that handles more power or uses alnico magnets. But in those instances where you’d like to preserve a vintage gem, like our pre-CBS 1964 Fender Super Reverb, I found the experience of listening to my old Jensens in rebuilt form well worth the time and expense. Check out Weber speakers at www.tedweber.com.